Volvo CE is blazing a new trail in its commitment to spare parts for its customers and new product development.
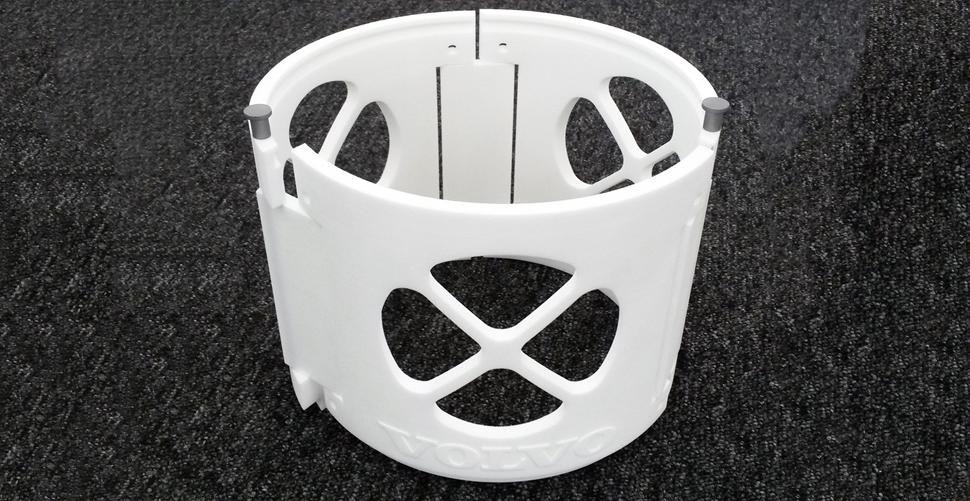
The construction industry is looking for new and efficient production methods, and equipment manufacturers are also looking for other ways to increase productivity. In order to provide spare parts to customers faster and more efficiently, Volvo CE has introduced 3D printing technology. In addition to this, the company has also invested heavily in 3D printing methods in the development of prototype machines.
“We support our customers throughout the life of the equipment, said Jasenko Lagumdzija, Business Support Manager at Volvo CE. This technology is particularly useful for older machines where parts have worn out and can no longer be efficiently produced using traditional production methods. Producing new parts by 3D printing can reduce time and cost, which is very helpful to customers. ”
Additive manufacturing is a big help to customers
Additive manufacturing, commonly known as 3D printing, is the process of repeatedly stacking molten material or liquid in a specific pattern set by the printer's software until it solidifies into the desired three-dimensional shape. For aftermarket services, Volvo CE commissions other companies to manufacture spare parts made of thermoplastics and then sends them to customers who need to replace parts that have worn out due to natural use.
Parts can be made in any shape and size and can be used on any unit in Volvo CE's off-road range. Typical parts manufactured so far by 3D printing include cab parts, plastic coverings and air conditioning unit components. The company uses its own drawings, 3D models and product information files to feed the printer with data to produce the right new parts.
“When you replace plastic with plastic, the customer gets an identical part,” said Annika Fries, Aftermarket Brand Manager at Volvo CE. “We have a lot of quality assurance processes, so the 3D parts have the same specifications and go through the same processes and warranty as the original product, so the customer can be assured that they are getting a genuine, Volvo-verified part.”
Fast and efficient response
It only takes one week to produce a new part through the 3D printing process. Providing the required parts quickly maximizes the uptime of the customer’s equipment; the ability to provide new parts to replace those that are out of normal production range also extends the overall life cycle of the machine. Metal parts produced through additive manufacturing will also be available in the future.
“We benefit from the fact that 3D printing can significantly shorten lead times and there are no minimum order quantities, so we can deliver parts faster, keep less inventory in our warehouses and balance supply and demand better,” said Daniel Kalfholm, Project Leader for Aftermarket Procurement at Volvo CE in EMEA. “And the purchase price is roughly the same as if the parts were manufactured in a traditional way.”
Prototyping takes it to the next level
In addition to its growing use in the production of aftermarket parts, 3D printing is also being used by Volvo CE to produce completely new parts for its prototype machines. The company’s R&D site has several 3D printers built specifically for this purpose.
“As we only need to produce a small number of parts for prototyping, it’s a good way to see if an part is useful,” said Fredrick Andersson, R&D engineer for powertrain installations on Volvo CE’s wheel loaders. We have a wealth of knowledge and can make changes quickly and easily with 3D printing. As a result, new products can be brought to market in a shorter time, which is a great benefit to our company. ”
Figure 1. The workshop tool used to install the accessory on the axle has been produced using 3D printing.